Fatigue testing is key to understanding why components or materials fail over time when subjected to repeated loading or stress cycles – which can lead to phenomena like cracking, pitting, micropitting, and other forms of damage.
Through exploring failure modes and performance under accelerated conditions, our customers can enhance product quality, innovate more rapidly, reduce costs, and gain a competitive advantage in their industries.
Fatigue testing in our lab allows us to simulate real world stresses in an accelerated timeframe, allowing us to then evaluate the performance of lubricants, materials and coatings on failure modes including Pitting, Micropitting and White Etching Cracks (WEC)
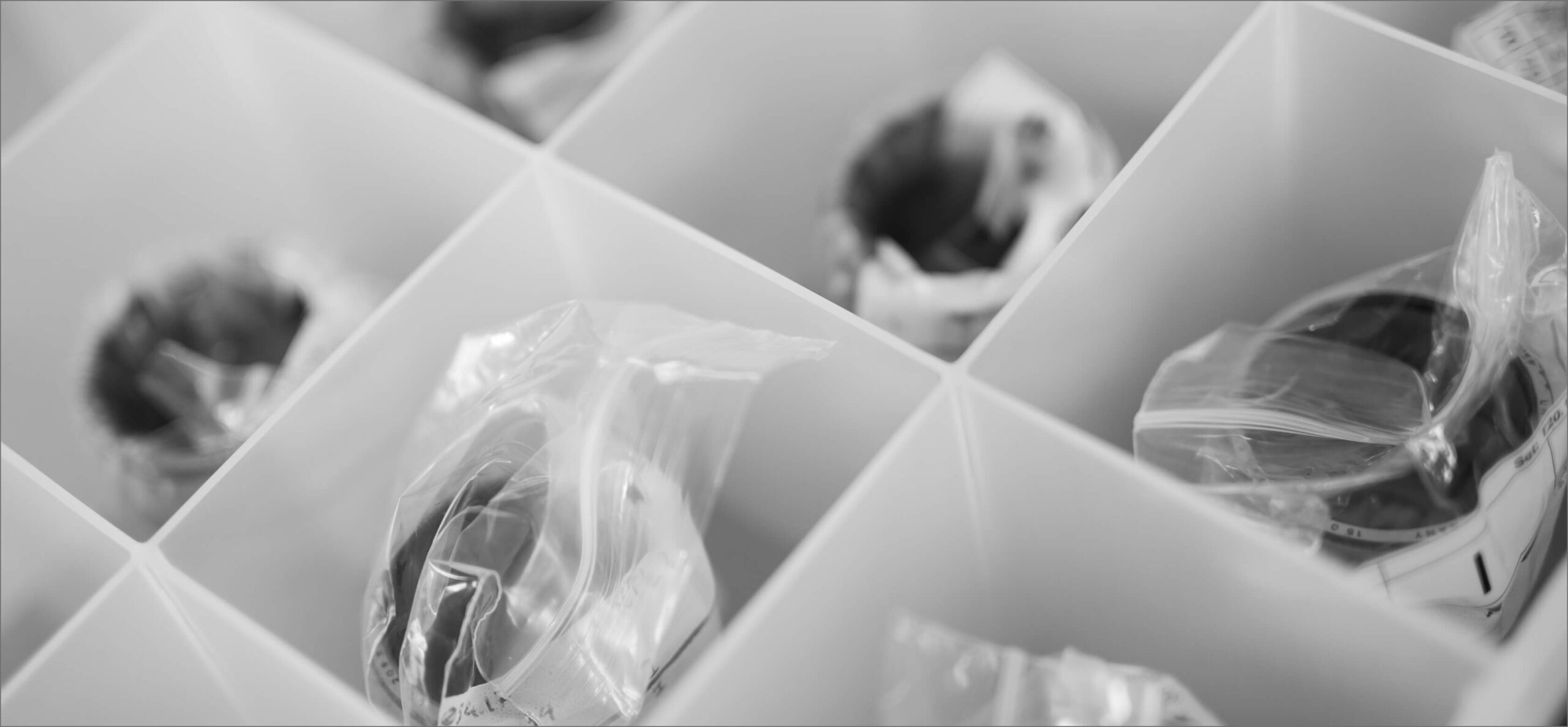
Fatigue Testing Process Explained
- Repeated Loading: Fatigue testing involves subjecting a material or component to a repetitive load or stress cycle. This cyclic loading can be similar to what the material would experience in real-world applications, like the constant flexing of an aircraft wing, the rotation of gears in machinery, or the vibrations in a vehicle’s suspension.
- Failure Analysis: The primary goal of fatigue testing is to determine how a material or component degrades and eventually fails over time due to these repetitive loads. It helps identify the critical points at which cracks, fractures, or other forms of damage initiate and propagate.
- Failure Modes: Common failure modes explored through fatigue testing include pitting (the formation of small cavities), micropitting (very fine-scale pitting), and white etching cracks (WEC, a specific form of cracking). These modes are particularly relevant in applications where components are subjected to high-stress cycling, such as gears in machinery, bearings, or critical structural elements.
Micropitting
Micropitting is a concern in gears and sometimes bearings.
Small pits are formed on the the surface of the material, leading to loss of geometry, and this micropitting frequently leads to pitting/spalling and eventually part failure. The material ejected by micropitting can also cause abrasive wear.
Surface treatments, materials and chemical additives can be used to reduce the occurrence of micropitting.
Through testing, we can accelerate this process and evaluate the performance, identifying the most effective ways of mitigating the problem.
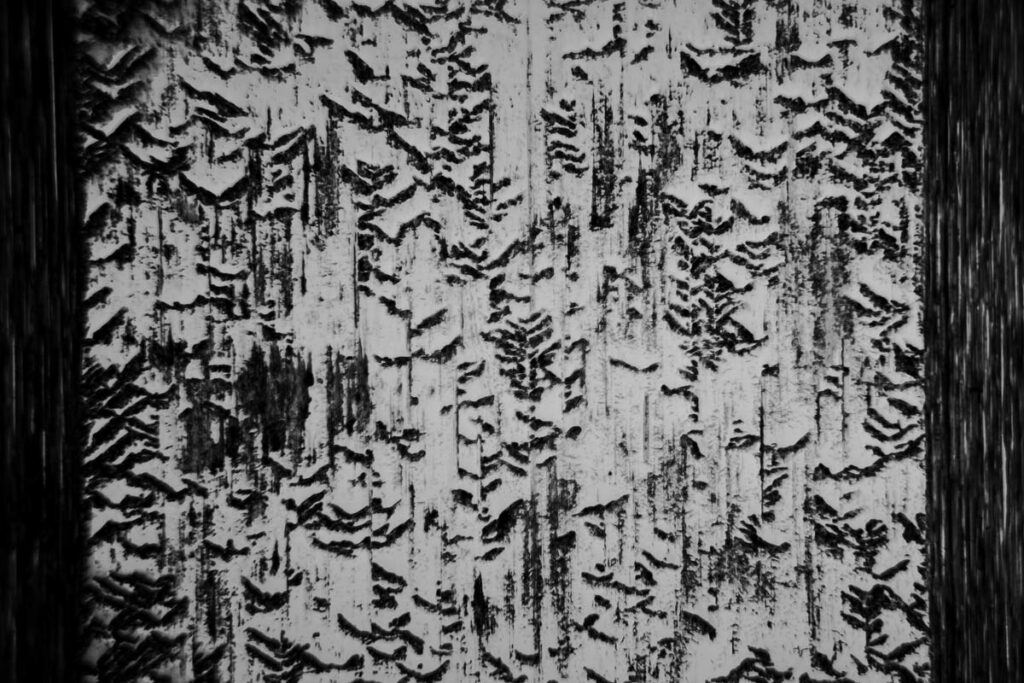
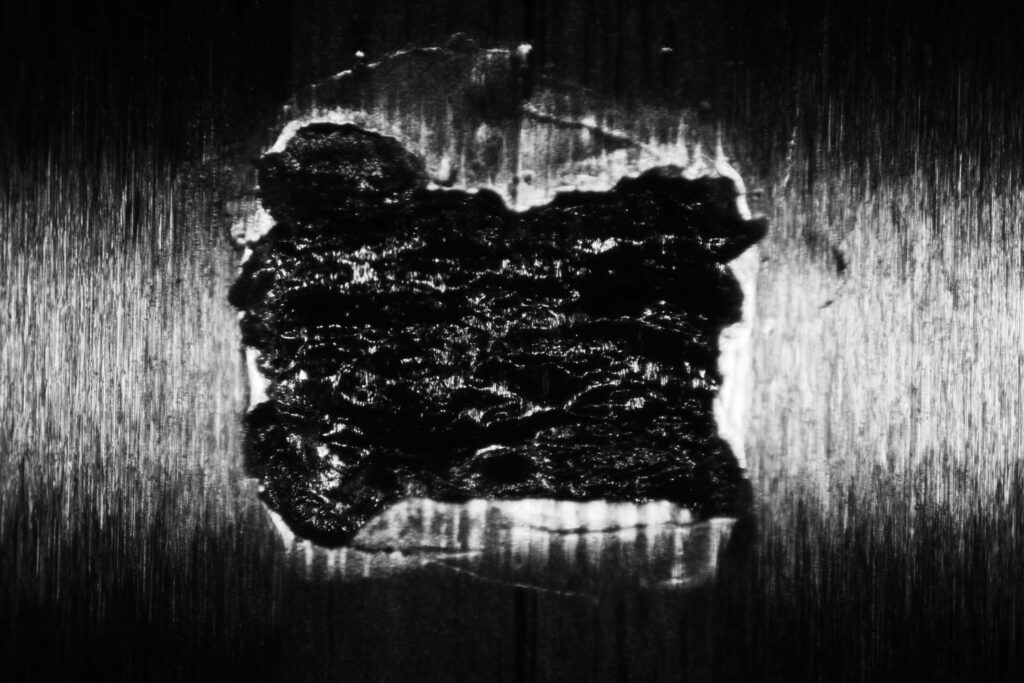
Pitting
Pitting, in contrast to micropitting, refers to single, larger pit being formed on the material. These pits can vary in size, potentially up to several centimetres in diameter.
This pitting typically occurs at the life of the machine, and indicates the failure of a part after a long period of operation. The high vibration and high noise caused by pitting can severely compromise the structural integrity of components, leading to reduced load-bearing capacity and potentially catastrophic failure.
WEC (White Etching Cracks)
White Etching Cracks are a type of subsurface initiated pitting failure of hardened steels – commonly observed in wind turbine bearings.
A subsurface crack is usually initiated on a metal inclusion, which then grows until it reaches the surface.
They are characterised by early failure by pitting and can be viewed directly with subsurface analysis – viewing below the surface area using a sectioning, grinding and etching procedure. The WECs are cracks surround by a white etched area.
We generate WECs on small rollers and conduct subsurface analysis to confirm their presence.
Image showing WEC network around a spall @ 100µm
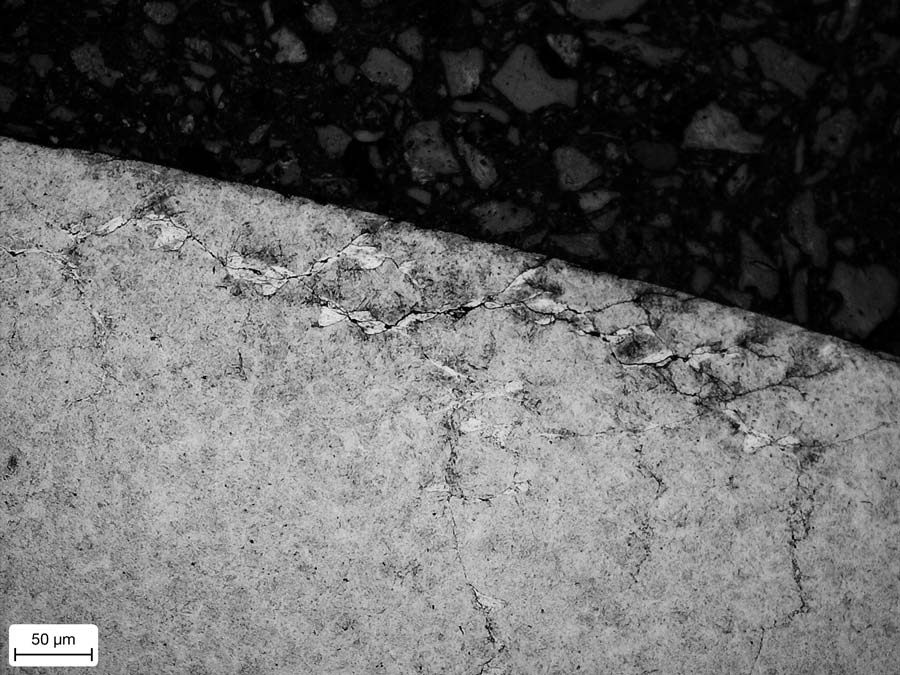
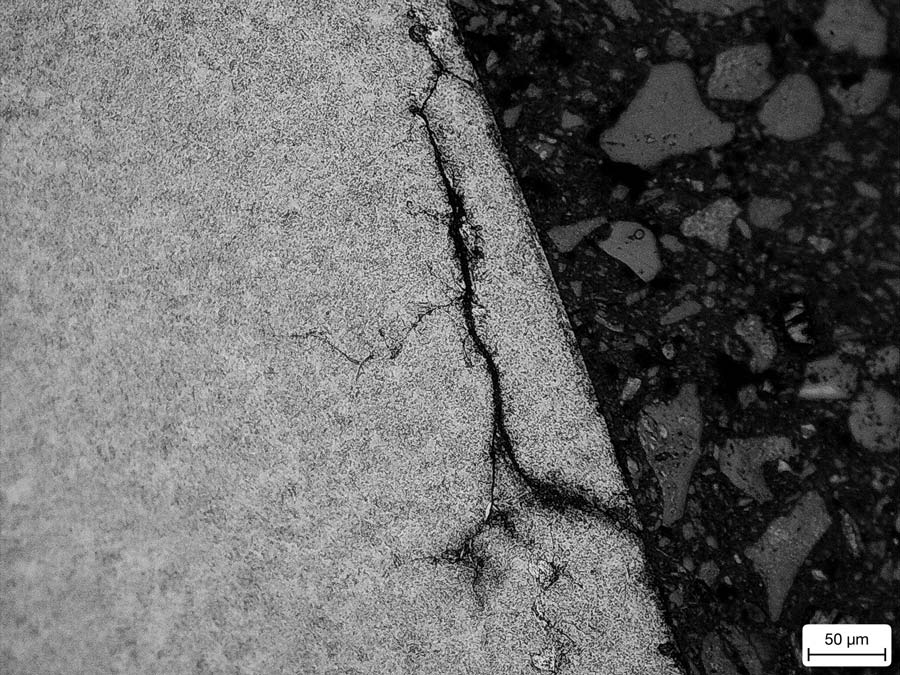
Surface and Subsurface Analysis
Frequently forming part of our Fatigue Testing, Surface and Subsurface Analysis allows us to look closely at the surface, and under the surface of the tested metal to better understand any failure mechanisms
A careful process of sectioning, grinding, polishing and sometimes chemical etching is used to view the surface and subsurface of the materials in steps.
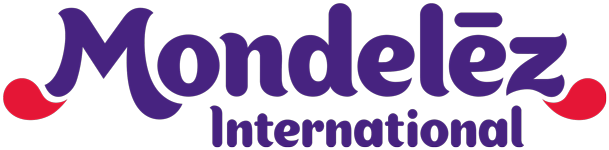
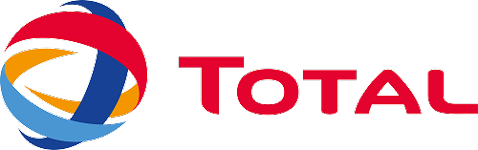
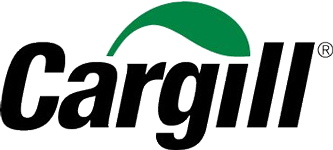
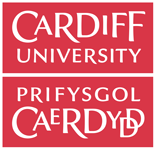
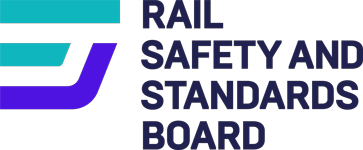