Surface and Subsurface analysis is a vital tool that allows us to unravel the causes of failures, shedding light on why and how materials deteriorate.
Through meticulous analysis, we explore both the outside and inside of tested samples, identifying imperfections and structural irregularities responsible for material failures – particularly WECs, pitting and micropitting. With this information, we’re able to construct a detailed narrative of the events leading to breakdown.
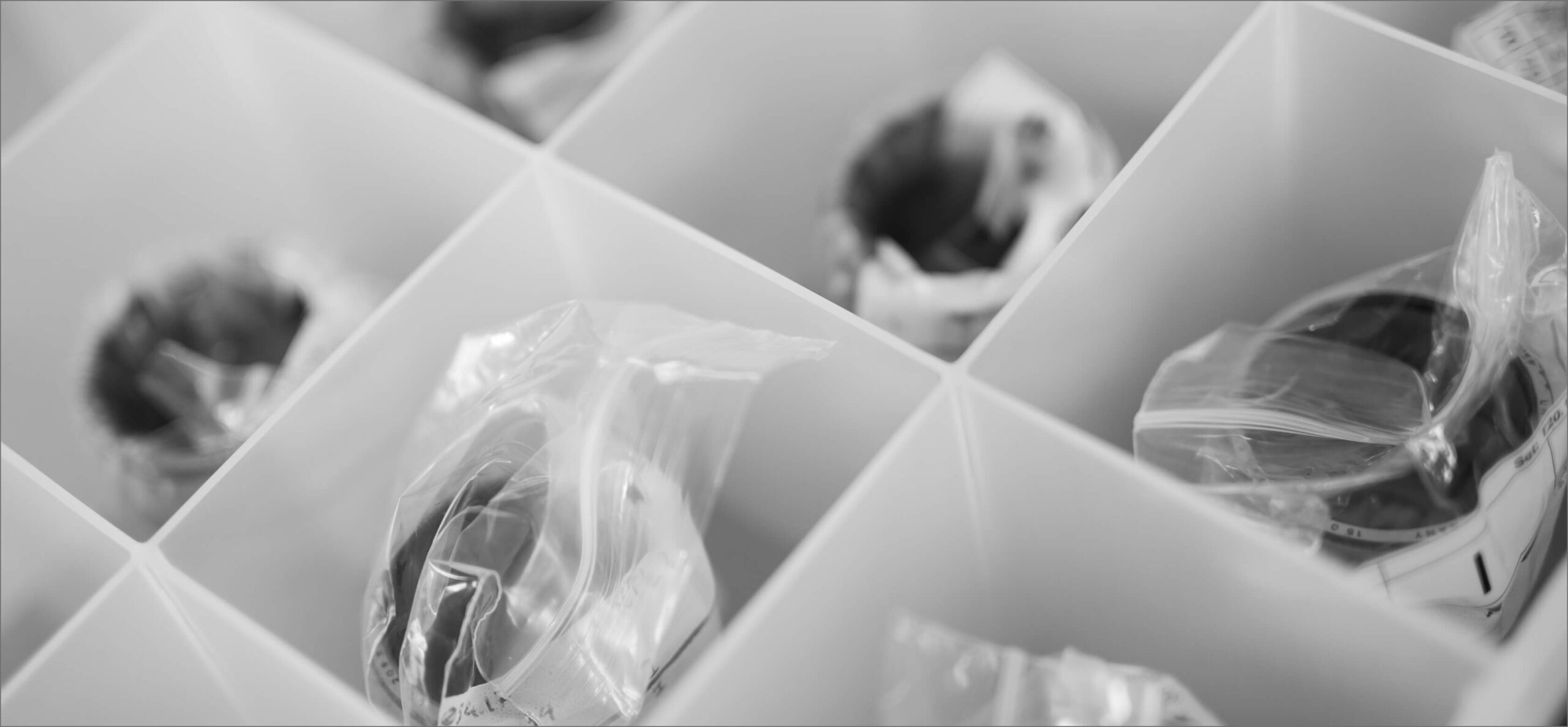
See under the Surface
When we subject material samples to testing, it’s not always evident whether they will withstand the conditions. Sometimes, even though samples appear visually sound, they might be on the verge of imminent failure.
Subsurface analysis offers a valuable advantage by allowing us to delve beneath the surface.
This enables us to identify and assess the presence of weaknesses, such as wear, erosion, or cracks, which may not be apparent from a superficial examination.
Analysis Techniques
Our surface and subsurface analysis employs a range of precision techniques to investigate samples. These methodologies include:
- Sectioning: This process involves precise sample preparation by carefully segmenting the test material. The cross-sectional samples created provide invaluable insights into the inner structure and composition.
- Grinding: A controlled abrasion technique is employed to systematically remove thin layers of the specimen. This gradual approach allows us to comprehensively assess the material’s properties and detect any surface irregularities or wear patterns at various depths.
- Polishing: Though careful polishing, we can provide better visibility of expose fine surface details that might otherwise be undetectable.
- Etching: Using chemical solutions to treat the material’s surface, we are able to accentuate microscopic features and provides a heightened level of contrast under a microscope – enabling the detailed study of surface characteristics.
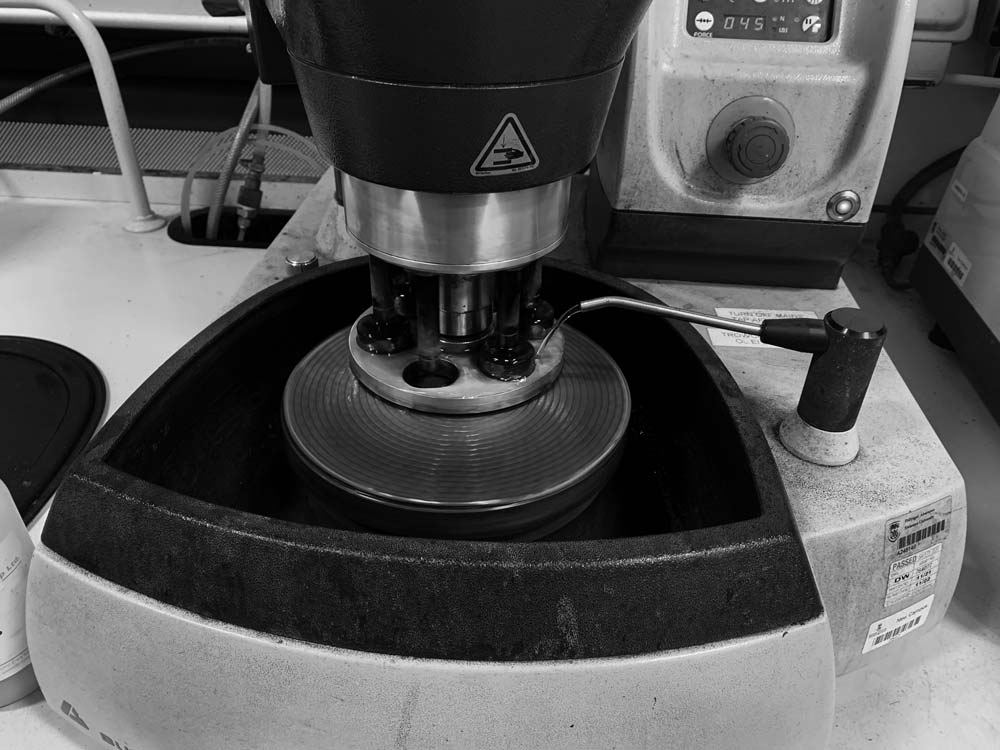
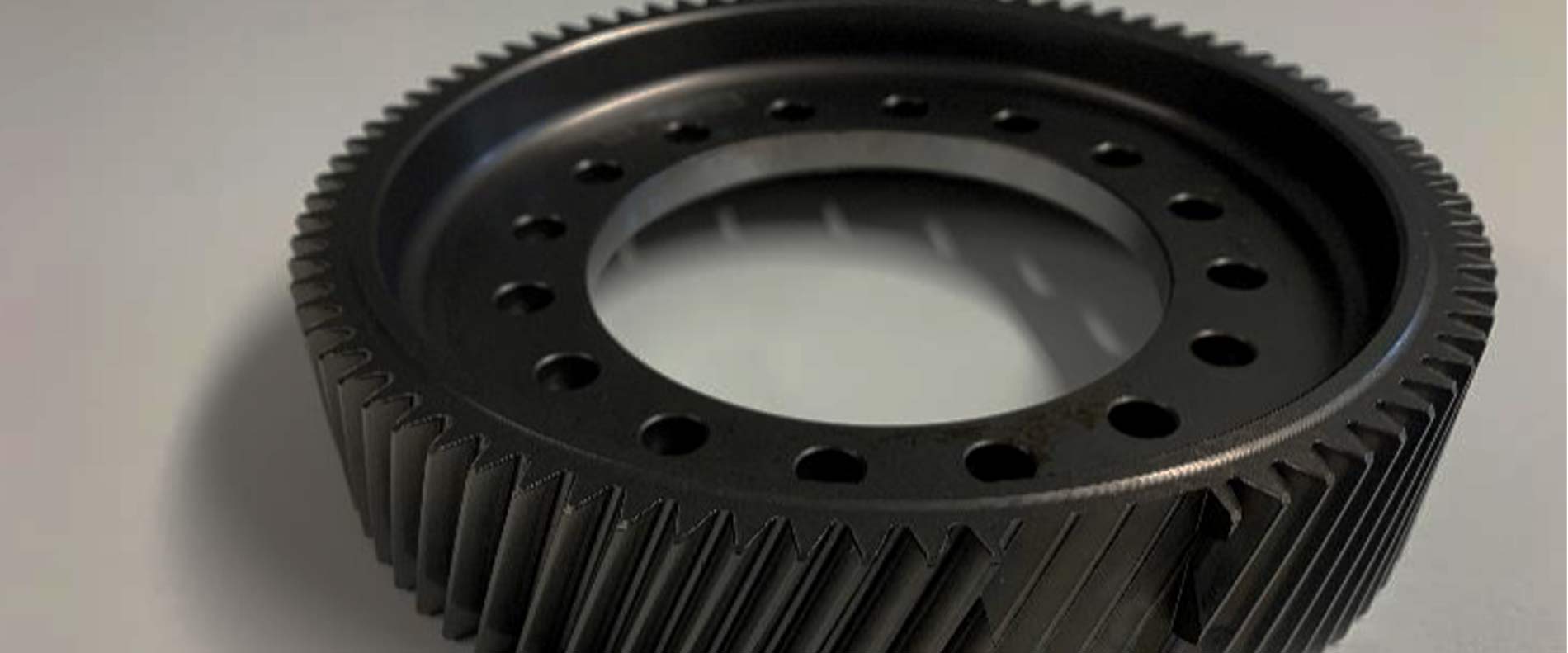
Case Study
Subsurface analysis of EV parts
A client was concerned about potential WEC failure on transmission bearings and, after the EV transmission had been through its normal testing, it was disassembled and sent to us for a thorough analysis.
We conducted a thorough subsurface analysis, looking for subsurface features such as butterflies, inclusions, and crack network.
The results gave the client confidence that they could prevent the formation of white etching cracks in the transmission – and that they weren’t lurking undetected, only for the part to fail when it reached service.
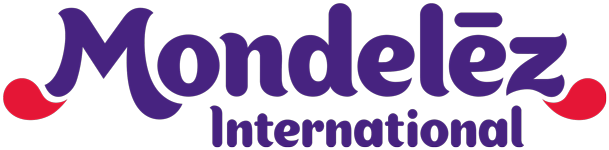
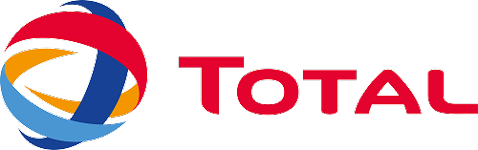
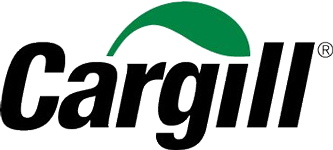
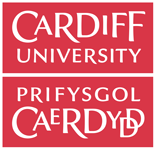
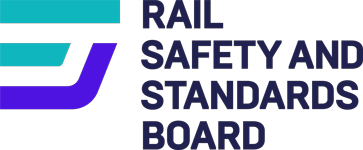