Research into materials and how they can be optimised is an integral part of product design and improvement across nearly every industry.
By measuring friction and wear, our engineers can understand how materials, coatings, and lubricants are affected by processes and find better solutions – improving reliability, efficiency and performance
Real World Applications
There’s a huge range of applications where Tribology can deliver competitive advantages. Find out how more about how we can use it to solve problems for key sectors.
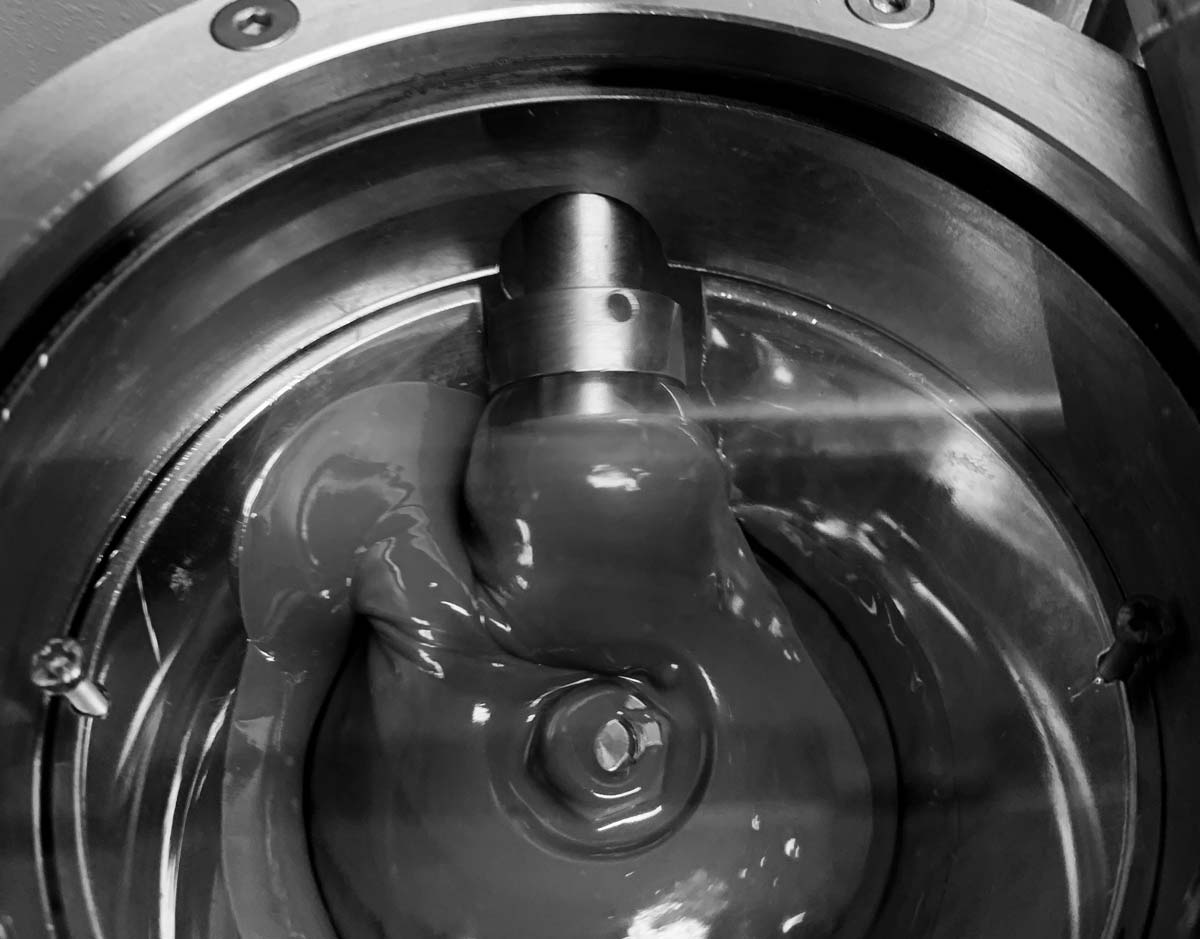
Food Production
Tribology is not just useful in mechanical applications – See how it benefits Food Science.

Wind Turbines
Solve problems with failure rates and improve efficiency with effective Tribology lab testing.
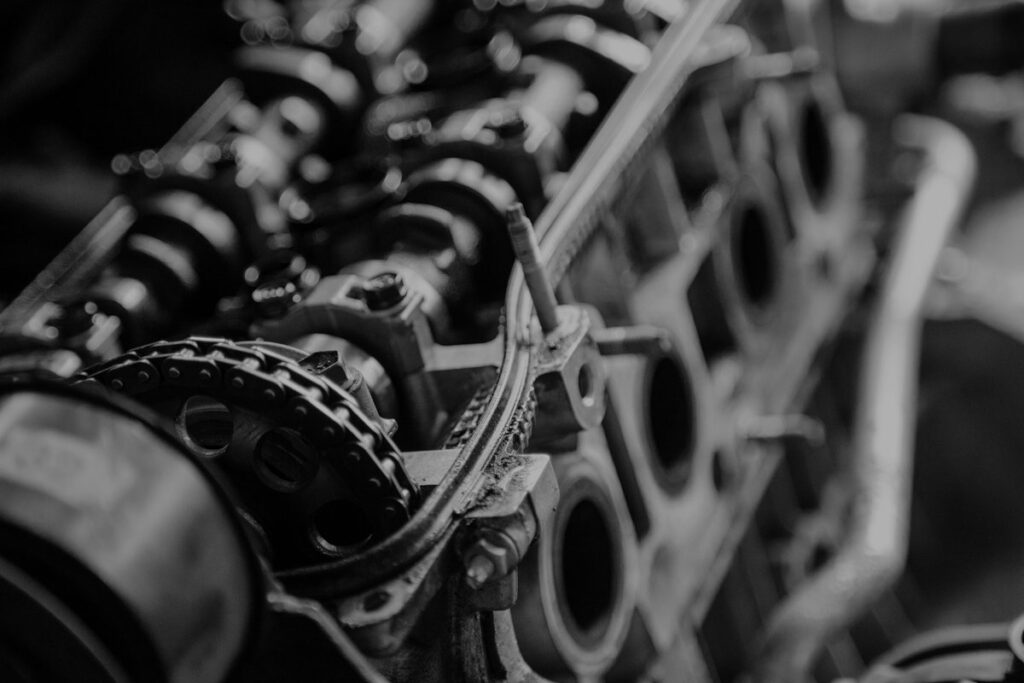
Engine Oils
From improving MPG to reducing wear, lubricant design can deliver huge benefits for engines.
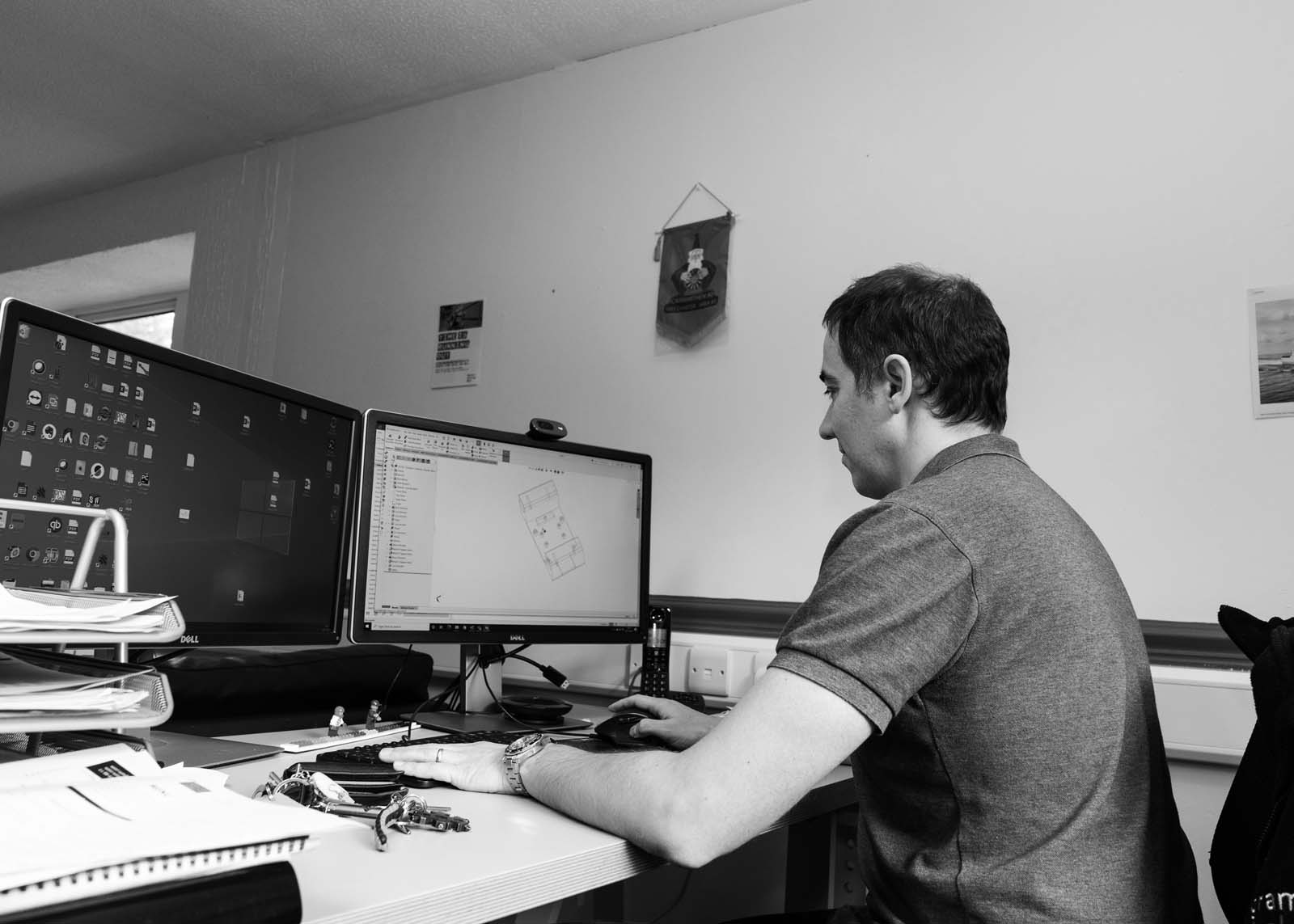
Computational Modelling
See how machine learning can translate tribology test results into real-world performance predictions.
“Ingram Tribology delivered high-quality results with great attention to detail and professionalism. They also met our deadlines and expectations with their fast and efficient service. We are grateful for their support and expertise”
Maruti Sai Dhiraj Sakhamuri, Ph.D. Researcher, University of Southampton
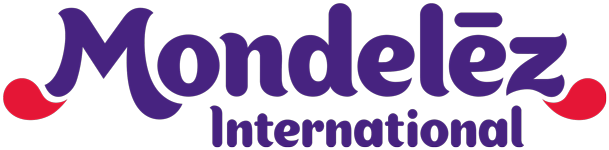
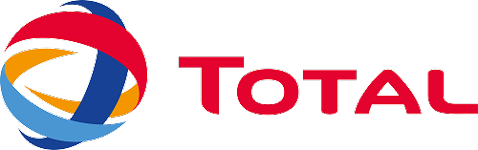
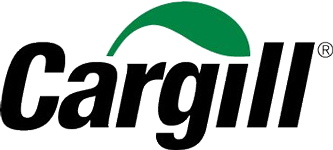
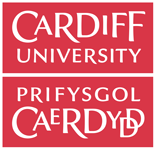
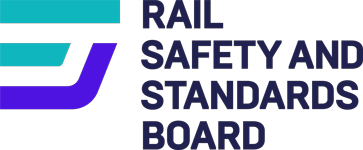
Tribological Thinking
Find out about our latest thinking, research, news and more.
-
Understanding the Science of Skin Feel: How Biotribology Shapes Cosmetic Perception
The global cosmetics market is valued at a staggering $700 billion per year, encompassing everything from skin creams and shampoos to shower gels and makeup. It’s a fast-paced industry where innovation is essential, especially as brands move toward more sustainable, vegan, and cruelty-free formulations. A product’s success isn’t just about what’s inside the bottle—it’s about…
-
🌟 Ingram Tribology Achieves ISO 9001 Certification! 🌟
We are proud to announce that Ingram Tribology has successfully achieved ISO 9001 Certification! This globally recognised certification demonstrates our commitment to delivering the highest standards of quality across all aspects of our operations. It reinforces our dedication to meeting customer and regulatory requirements, and ensures that we continually improve our processes to provide the…
-
Introducing Our New Course: Bio-Tribology for Industry
We are excited to launch our latest training course: Bio-Tribology for Industry—designed specifically for researchers and product development scientists in the food, beverage, cosmetics, and medical industries. Why Take This Course? Understanding bio-tribology is essential for developing high-performance products that interact with the human body, whether it’s optimizing the feel of a skincare product, improving…
-
🚗⚡ Inspiring Future Engineers with Greenpower! ⚡🚗
The Greenpower Trust is an incredible charity that sparks excitement for STEM careers by giving young people the opportunity to design, build, and race their own electric cars. At Haverfordwest High VC School in Pembrokeshire, an all-female race team is gearing up to compete in the F24 Greenpower series—and we had the privilege of supporting…
-
Installation of new electrified MTM at Ingram Tribology ⚡ 🚃 🚘
We have expanded our testing capabilities with the addition of the new MTM-EC (mini traction machine electrical current)! This new instrument allows us to study the effects of electrical currents on lubricated contacts. In our growing electrified world, stray electrical currents can flow through mechanical devices. If the current is high, fluting damage can occur at the…
-
Introducing our new testing capability: tackling Electrically induced White Etching Cracks (eWECs)! ⚡🔬 🚗 👨🔧
In today’s increasingly electrified world, machine elements are often located near electric motors and generators, where they can be exposed to stray currents. Electric vehicles and wind turbines are prime examples of where this issue can arise. These stray currents can significantly impact tribological contacts, accelerating subsurface alterations in the steel and leading to premature…
-
Gear Micropitting Screening Test
Micropitting is a type of fatigue wear commonly found on gear teeth. The gradual loss of material in the form of small surface pits leads to a change in the geometry of the component; if this is not controlled, it can result in failure of the part. The standardised method of evaluating a lubricants ability…
-
Merry Christmas from all of us at Ingram Tribology
Our Christmas card this year depicts the scene of Santa enjoying the drinks left out for him near the fireplace. Santa is trying both port and hot chocolate and notices a distinct difference in the mouthfeel between the two. The port has a drier, thinner feel. Whilst the hot chocolate impacts a smoother, creamier feeling. …
-
Check out our first Tribo Gatherings Podcast
We have started a Podcast! Our first guest is Dr. Connor Myant from Imperial College. We discuss biotribology, as related to the testing of food and hip joint failures. We discuss the advances in 3D printing and how Connor moved from Tribology into 3D printing. We discuss all Connors current projects and thoughts for the…